Winter 2021, January Edition: Newsletter 04
Pipeline Integrity Management Program: Selection and Implementation

Guidelines on Pipeline Integrity Management (PIM) programs have been provided by regulations [e.g., by Pipeline and Hazardous Materials Safety Administration (PHMSA), Canadian Energy Regulator (CER), and Alberta Energy Regulator (AER)], standards [e.g., NACE SP 0113: Pipeline Integrity Method Selection], and industry best practices [e.g., Canadian Association of Petroleum Producers (CAPP) and Canadian Energy Pipeline Association (CEPA) best practices].
The PIM program may include 5-M Methodology, in-line inspection (ILI), direct assessment (DA), and pressure testing. These methodologies address several threats including internal corrosion (IC), external corrosion (EC), stress corrosion cracking (SCC), mechanical damage by either third party or vandalism, equipment damage due to manufacturing errors, construction practices, incorrect operations, weather forces, and other external forces.
The weakest linkage in implementing PIM is the collection of appropriate data and make them available at appropriate time to appropriate people. By integrating data collection and decision making, using appropriate software such as STEM_Risk Pipeline TM , PIM program can be effectively implemented in the industry
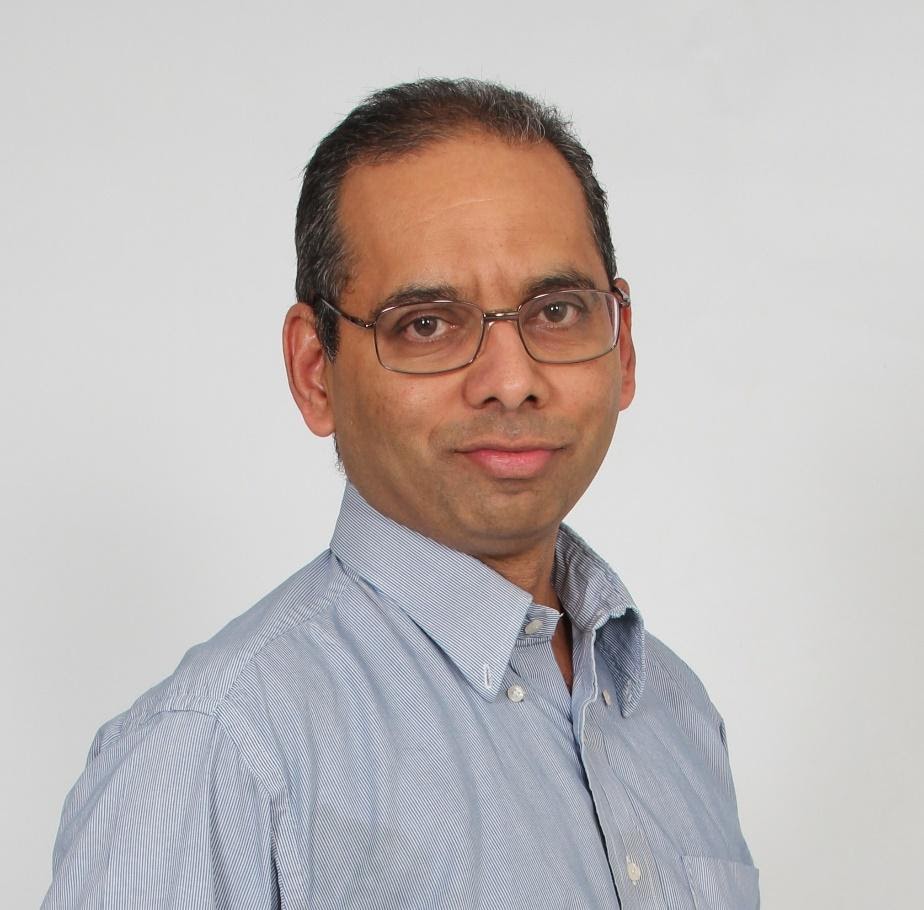
My Story
I was conducting research in India on how corrosion inhibitors and coatings present on the metal surface withstanding the influence of flow. In 1994, Winston Revie introduced me to the Canadian oil and gas industry and I live here ever after! .
My Style
The glass is always full - sometimes with water or sometimes with air! Help the clients to take informed decisions with what they have and help them to improve on. .
Pinnacle Moment
When I was able to convince policy makers, newspaper agencies, and general public that crude oil is not corrosive under pipeline operating conditions.
Greatest Contribution
Development of the 5-M (Modeling, Mitigation, Monitoring, Maintenance, and Management) methodology to effectively and economically control corrosion and development of software products (in collaboration with Interlace) for easier implementation of it.
Advice to Industry
By collecting and evaluating the data in the standardized manner, the corrosion cost may be reduced by 30% without increasing the risk. This approach will enable corrosion professionals to "lead" corrosion control rather than "follow" corrosion.